For the producers, manually inserting 18 brass female connectors into a plastic frame for a control unit was a laborious and costly process. Ultrasonic welding offered an efficient alternative which considerably shortened the cycle times and was also financially worthwhile – in spite of a low unit count. The versatility of the sonotrode and Herrmann Engineering played a crucial role here.
The challenge
- Production times of more than three minutes per part made the production of a plastic frame uneconomical for apra-plast.
- The reason behind the long cycle times was the total of 18 brass female connectors which had to be inserted into the frame individually using heat.
- An automated process was not worthwhile due to the low number of units.
Our solution
- Development of a special blade sonotrode to reduce cycle times.
- Provide a quick tool change system so that the ultrasonic welding machine can be used for other applications.
To speed up the production process, we first developed a special sonotrode which can insert all female connectors simultaneously and precisely for each side of the frame. This way, we were able to reduce 18 stages which were previously required for the complete frame to just four stages.
At the same time, the ultrasonic welding machine was designed so that it could also be used for another application of the customer. This involved welding a viewing window into the plastic housing of a measuring device. Previously, these viewing windows were glued, and the quality of the end products suffered as a result. Ultrasonic welding offered a process-reliable alternative here that guaranteed a flawless appearance.
Customer benefit
The developed welding solution makes it clear that the use of ultrasonics is also worthwhile if you produce small batch sizes. The prerequisite for this is in-depth support over the full duration of the project so that a versatile machine can be developed.
Particularly when compared to manual joining processes, ultrasonic welding offers the big advantage of faster production times and increased product quality, meaning that clients can design entire manufacturing processes to be more economical, sustainable and efficient.
Consulting as a success factor
With the two developed solutions, apra-plast is working with ultrasonic welding technology for the first time. In-depth basic training on ultrasonic welding and consulting with regard to the financial and technical feasibility of the project were crucial to the decision. By leasing a machine, the customer was able to perform tests in-house under real production conditions, and familiarize themselves with the use of the technology in advance.
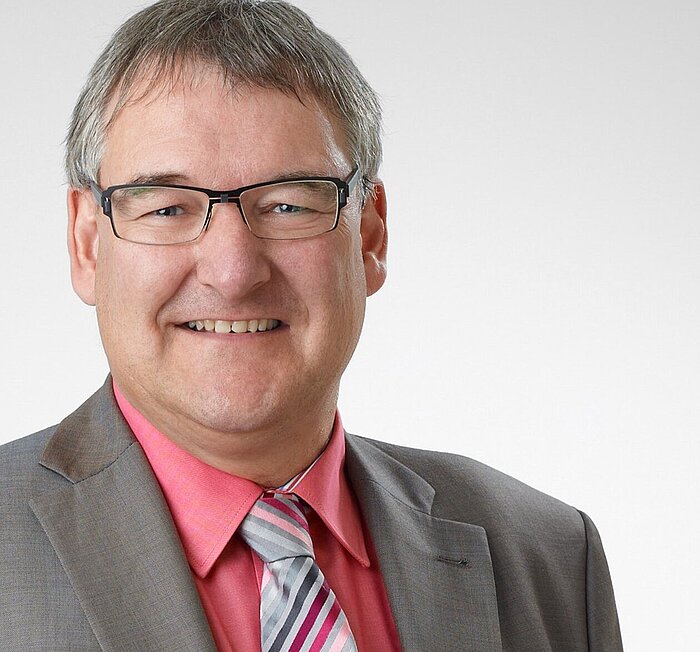
"The cooperation with Herrmann, especially in the context of finding solutions, was a lot of fun. We were very well advised and supported here.
The developed solution fulfills our wishes and requirements. New approaches have already been developed for which we will again receive competent support."
Juergen Koenen, apra-plast
From the first idea to the development of an application right up to process optimization, we will work out the best possible solution with you, hand-in-hand.
Use our know-how and optimize your projects too!